Data insights.
Gaining insights into your manual operations
- Insights into production processes and operator efficiency through real-time dashboarding
- Easy integration with MES/ERP systems
- Extend with your own custom dashboarding
“Data is key” – Insights in your manual operations
For manufacturers it is essential to improve all aspects of their operations. Therefore, it is crucial to create insights in the processes, systems and machines, allowing the manufacturer to collect valuable data and give him more ways to analyze the operations. These data can as such enhance productivity and performance, ensure product quality, optimize decision-making and lower costs, which are all essential aspects in his drive towards Industry 4.0. Most manufacturers are able to capture data from their automated processes (sensors, IO, PLC, robots, drives, etc.) but they are still collecting data from log sheets or operator displays for their manual operations.
With the Arkite platform, manufacturers are now also able to capture relevant information regarding the manual operations in their facility. Every manual assembly or picking task will be logged with the corresponding timestamp, allowing the manufacturer to perform time studies, line balancing and process improvements. Additional parameters and variables can be stored. This will give manufacturers more insights into their production processes and the way the product has effectively been made by their workers.
Arkite’s standard ‘out-of-the-box’ dashboards provide manufacturers the tools to deep-dive in their production processes. Reports, such as ‘Workstation Status’, ‘Product Output’, ‘Cycle Times’ and ‘Current Step Duration’, are automatically generated and readily available in the Arkite software. Manufacturers can further use the generated data in their own reporting tools such as BI reporting or any MES/ERP platform, creating additional insights regarding quality and efficiency. The Arkite Operator Guidance platform gives the manufacturers now the combined information of their automated – and manual operations, which is essential to further optimize processes across the manufacturing plant.
PCB assembly
for usage in aerospace applications
- Barcode scanner integration for selecting product variants
- Full Traceability through connectivity with Oracle backbone
- Paperless environment through digital AR work instructions
- Smart Tool Integration
- On-the-job training of operators
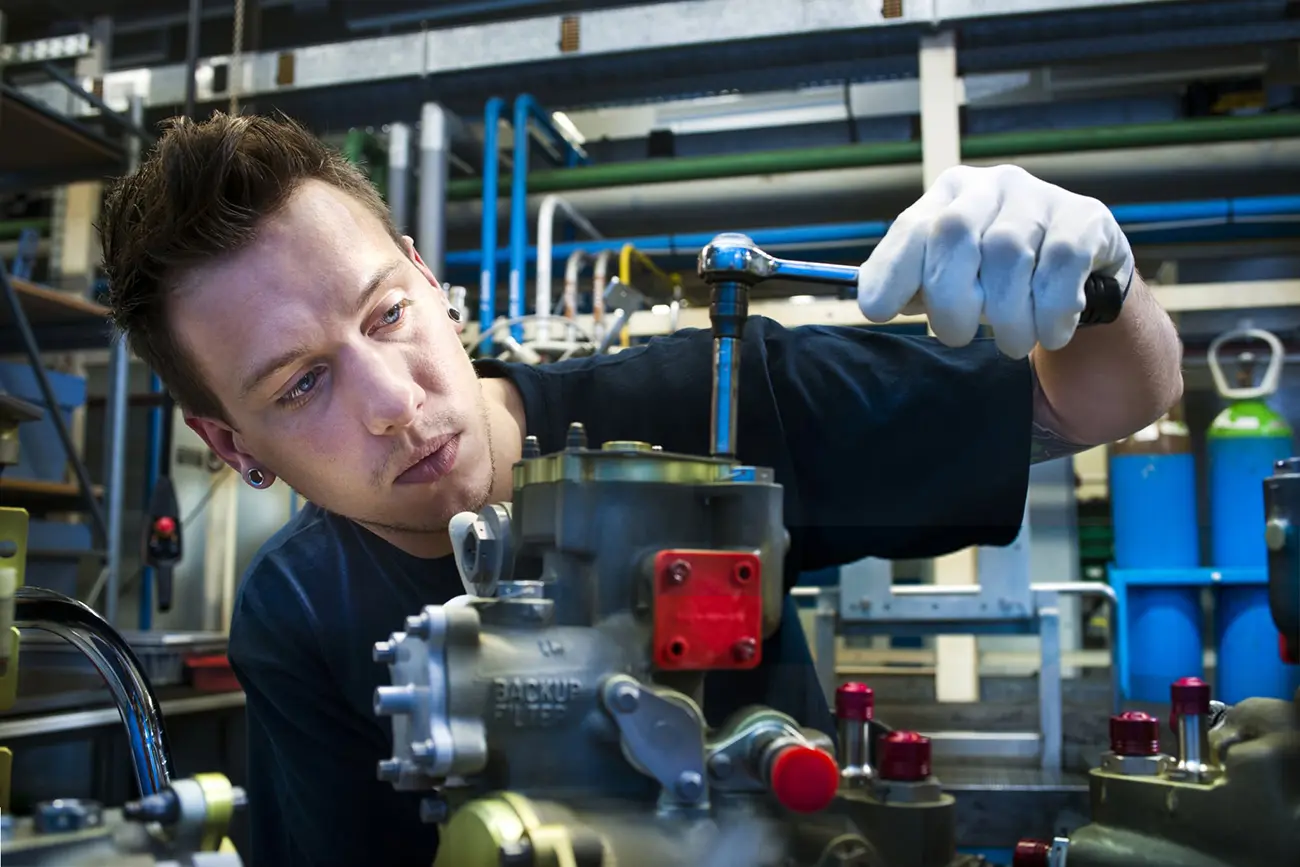
Arkite's operator guidance platform was installed at a manufacturer of communication modules or the International Space Station (ISS), consisting of printed circuit boards. The manual assembly of these modules is characterized by a high complexity, long cycle times, a high number of variants and a low volume per product variant.
The Arkite system guides the operator step by step in the picking and assembly process with digital Augmented Reality instructions projected in real-time on the workstation or the product itself.
It is fully integrated into the customers IT eco-system.
Arkite’s Operator Guidance platform transforms your manual workstations into a digital environment by deploying Augmented Reality.
It will give you the control and insights to efficiently steer and optimize your manual assembly processes.
Other solutions
Arkite’s Operator Guidance platform can help you find an answer to the challenges that arise in today’s highly competitive market. By deploying Augmented Reality on your factory floor, you transform your manual workstations into a digital and interactive environment that allows you to efficiently transfer knowledge to your operators. Thanks to the seamless integration in your company’s ecosystem, our platform will also provide you with the required information to optimize your assembly process.
Explore the details of our solutions, or click the contact button below to find out more.
FLEXIBLE PRODUCTION
KNOWLEDGE PRESERVATION AND ONBOARDING
PAPERLESS WORK ENVIRONMENT
CABLING/WIRE HARNESSES
PICKING AND KITTING
TIGHTENING
TRACEABILITY
STANDARDISED WORK
ASSEMBLY
Improve your
manual operations
with better
consistency
and reliability
%
error reduction
%
rework reduction
%