Complex PCB assembly for usage in Aerospace
Our customer is a world-class supplier for the aerospace industry, responsible for the design, manufacturing and delivery of critical components for satellite based systems. They are also the manufacturer of several modules for the International Space Station (ISS).
Their portfolio contains specific communication modules, consisting of printed circuit boards. The manual assembly of these modules is characterized by a high complexity, long cycle times, a high number of variants and a low volume per product variant. To increase the quality and traceability of the picking and assembly process, the customer was looking for an operator guidance technology.
The specific characteristics of the assembly process led to a high risk for human errors:
- Operators had to find their way into a large amount of information, such as Standard Operating Procedures, paper manuals and CAD drawings, to find the correct instructions for a specific process step for a specific variant. Delays in production and assembly errors were caused by the use of wrong or outdated instructions.
- The long cycle times made it very challenging for operators to keep their focus and avoid mistakes.
- The high product variety demanded for frequent and extended trainings, and even then also the most experienced operators still occasionally confused between product variants.
Since safety and quality is of the greatest importance in aerospace, every single error causes a significant cost. Therefore, our customer considered it to be fundamental to reduce errors to the absolute minimum.
Furthermore, Arkite’s is fully integrated into the customers IT eco-system. As a result:
- full traceability of every process step was accomplished through connectivity with the Oracle backbone.
- the integration of a barcode scanner allows the operator to select the correct product variant in the beginning of the assembly by simply scanning the corresponding barcode. In this way, errors related to confusion between product variants can be fully excluded.
- the integration of smart tools (screwdrivers and torque tools) assured components are tightened with the correct torque and tools are used at the expected physical location and in the correct sequence of the assembly process. At all other times and locations, the tools are disabled by the Arkite software.
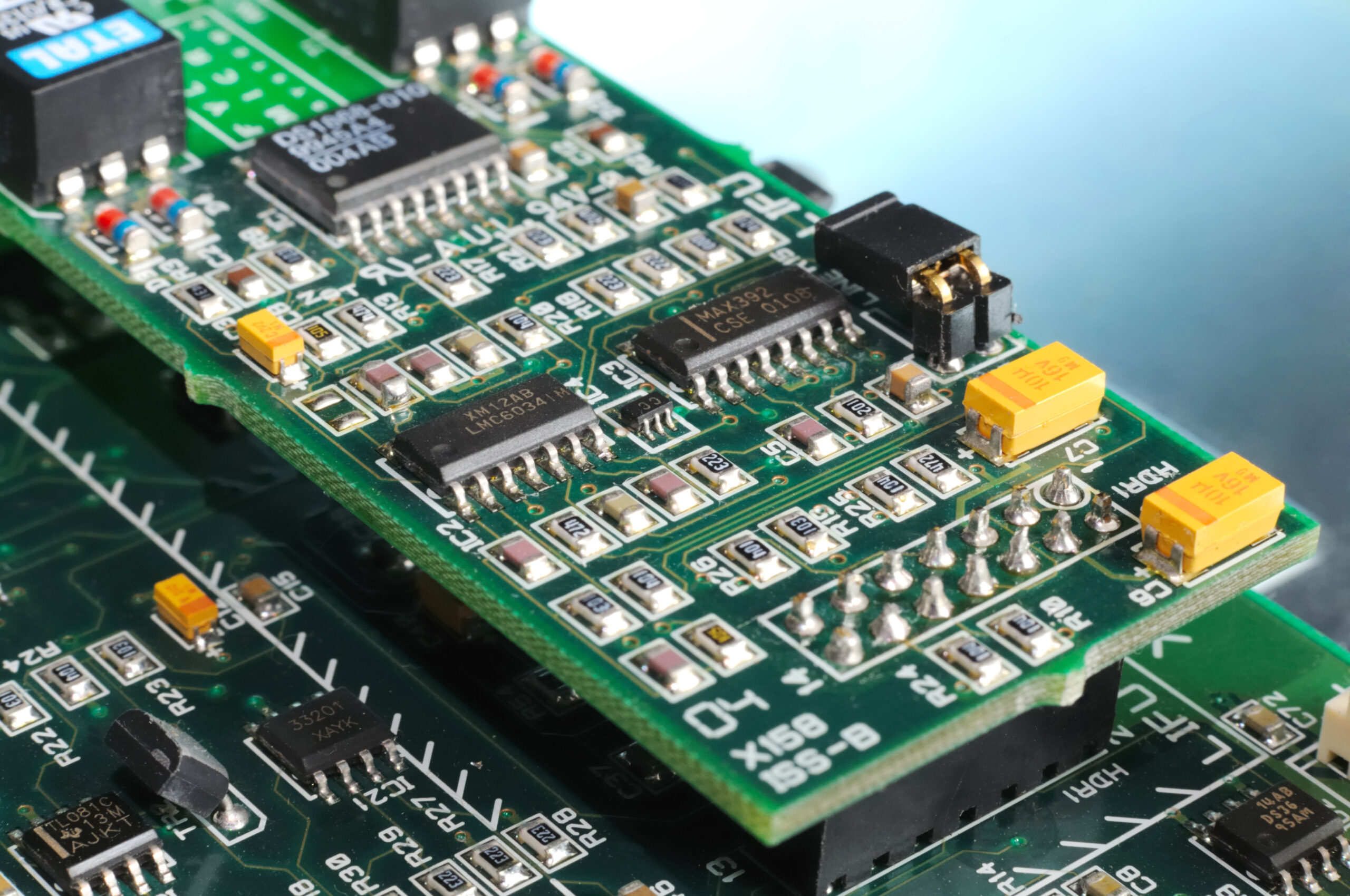
Arkite installed its operator guidance platform, consisting of an Arkite 3D smart sensor and a projector, on the customer’s work floor. Our project team translated the assembly process into the software. After implementation, the Arkite system guided the operator step by step in the picking and assembly process with digital Augmented Reality instructions projected in real-time on the workstation or the product itself. As a result, paper procedures could be completed omitted. Every action is also validated with the smart sensor, allowing the system to detect errors and warn the operator before proceeding to the next step.
As a final outcome, the Arkite operator guidance platform helped our customer reached its high quality objectives, reducing production errors to almost 0. Additionally, by providing operators with the right information at the right time, a standardized way of working could be implemented and enforced.
Our solution also facilitates the integration of new employees. It acts as an on-the-job trainer, reduces the need for supervision and thus allows to deploy workers in assembly operations much faster. Additionally, the Arkite system increases the operators’ job satisfaction. By giving him the assurance he needs, the platform reduces the perceived complexity of the assembly process.
Today, the customer configures and maintains the Arkite solution themselves. The engineers appreciate not only the features and capabilities of the product but also its ease-of-use.
Are you curious about what Arkite’s operator guidance platform can do for your organization?
- Visit our website to learn more about our product and customer references
- Request a free live demo
- To know more about the technology used by Arkite, navigate to http://documentation.arkite.com and download our FAQ and Technical Information